Fill, seal, done
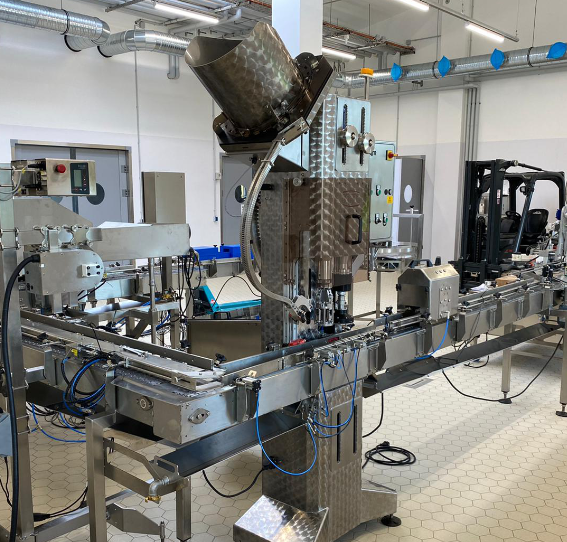
Filling and capping
Task definition:
A customer was looking for a filling line for liquids in small shot bottles and wide-mouth jars with herbal products or chunky products. The requirements included a filling line for two different containers: Wide-mouth twist-off jars (approx. 250 ml) and shot bottles (approx. 60 ml). The wide-mouth jars had to be turned first. It was necessary to integrate a gear pump for filling the shot bottles and a capper for short screw caps and large twist-off caps. Furthermore, a washing tunnel was to be integrated, and due to the limited space available, a U-shape was necessary for the layout of the system.
Objective:
The objective was to fill 200 ml shot bottles with PP28 closures and 230 ml herb jars with TO82 closures. A large feeding table was to simplify the placement of the bottles. The wide-mouth jars had to be rotated 180° before filling to ensure that no particles remained in the jar. The jars were to be filled with herbs at two stations. Two gear pumps were to be integrated for filling the liquid (brine). A capper was to screw on both PP28x18 aluminium roll-on closures and twist-off 82 lids fully automatically. These had to be preheated due to the BPA-free seal. A small washing tunnel was used to remove any residue from the bottles before they were pushed onto a labelling machine with a collection table. The machine layout had to be selected such that the bottles could be loaded and unloaded in the grey area (hygiene area) and the products filled in the white area.
Solution:
The system was implemented in a classic U arrangement to ensure separation into white and grey areas. After a round feeding table, a jar turner was installed through which the wide-mouth jars were turned by dynamic pressure alone. A laner device separated the bottles on two tracks and then pressed them onto a herb/stopper table from below using pneumatic cylinders. After the bottles had been filled manually, they were released by foot pedal and passed through the bottle filling system with the two Fillogy gear pumps. Conversely, the bottles passed the herb/stopper table and were filled after a 90° bend in two lanes. Afterwards, jars and bottles were properly closed back on a track after another 90° bend under the TV2000TS with twist-off lids or PP28 aluminium lids. After passing through the washing tunnel, they then moved on to the labelling machine.
Download
Gallery
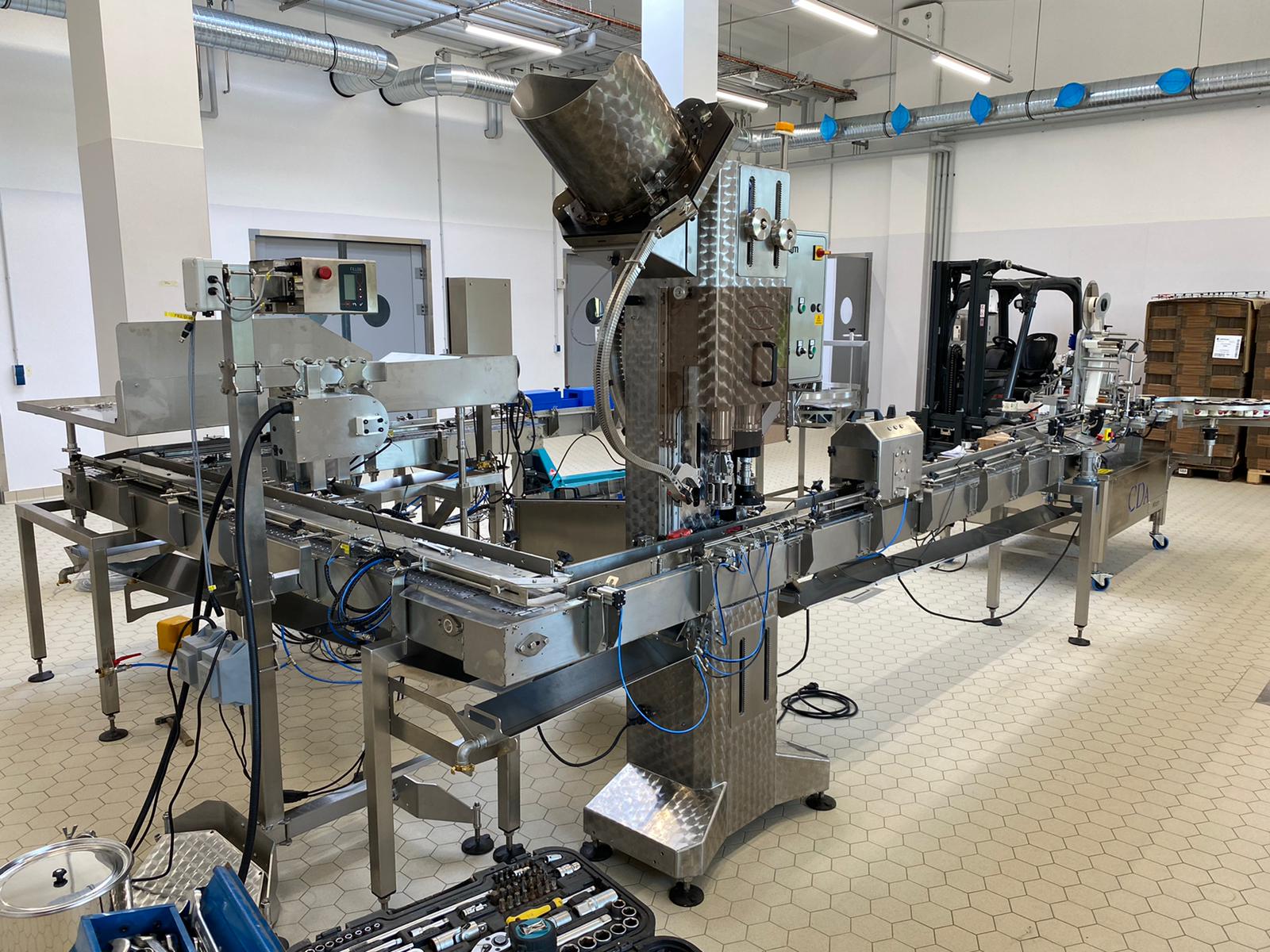
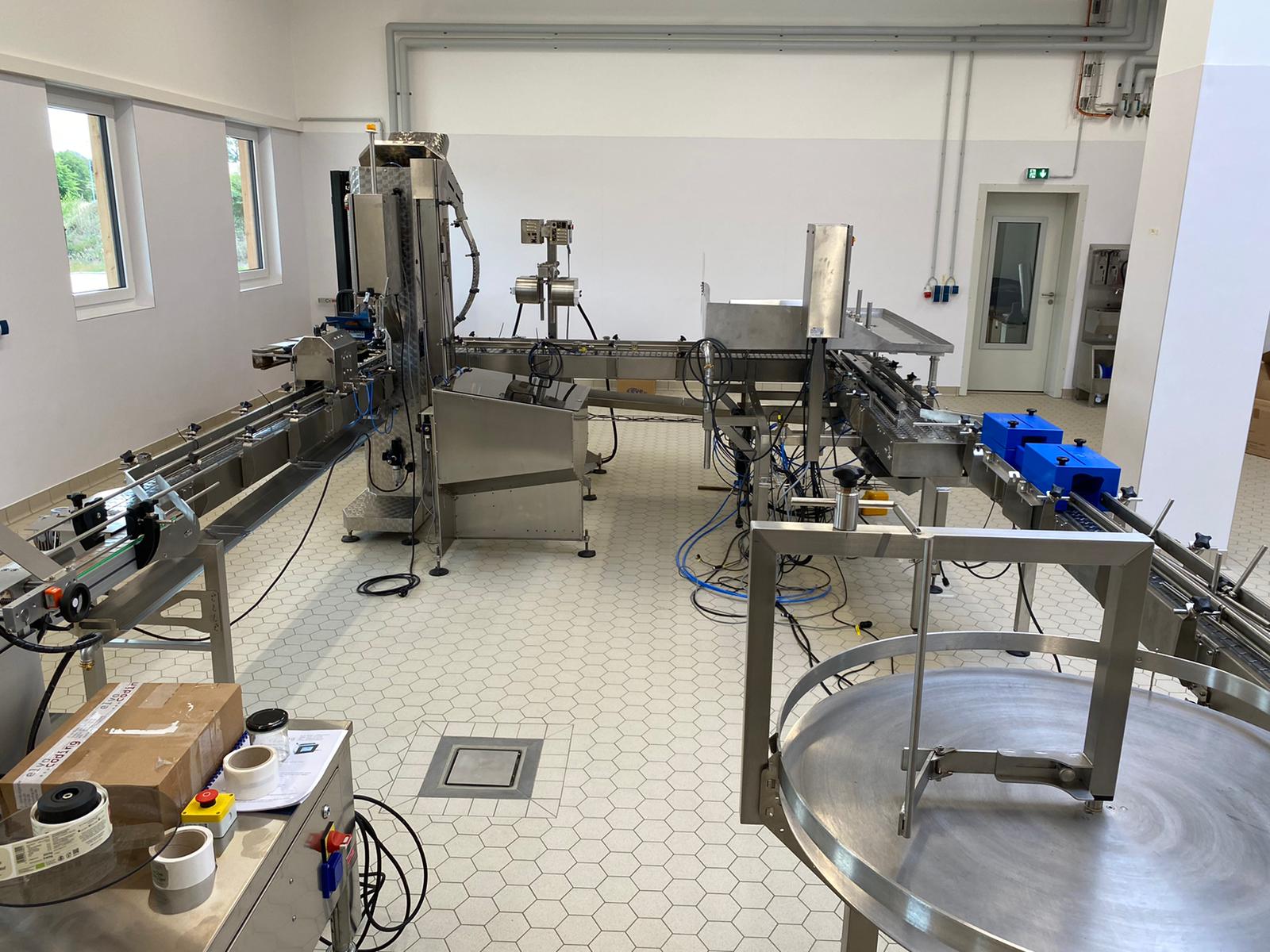
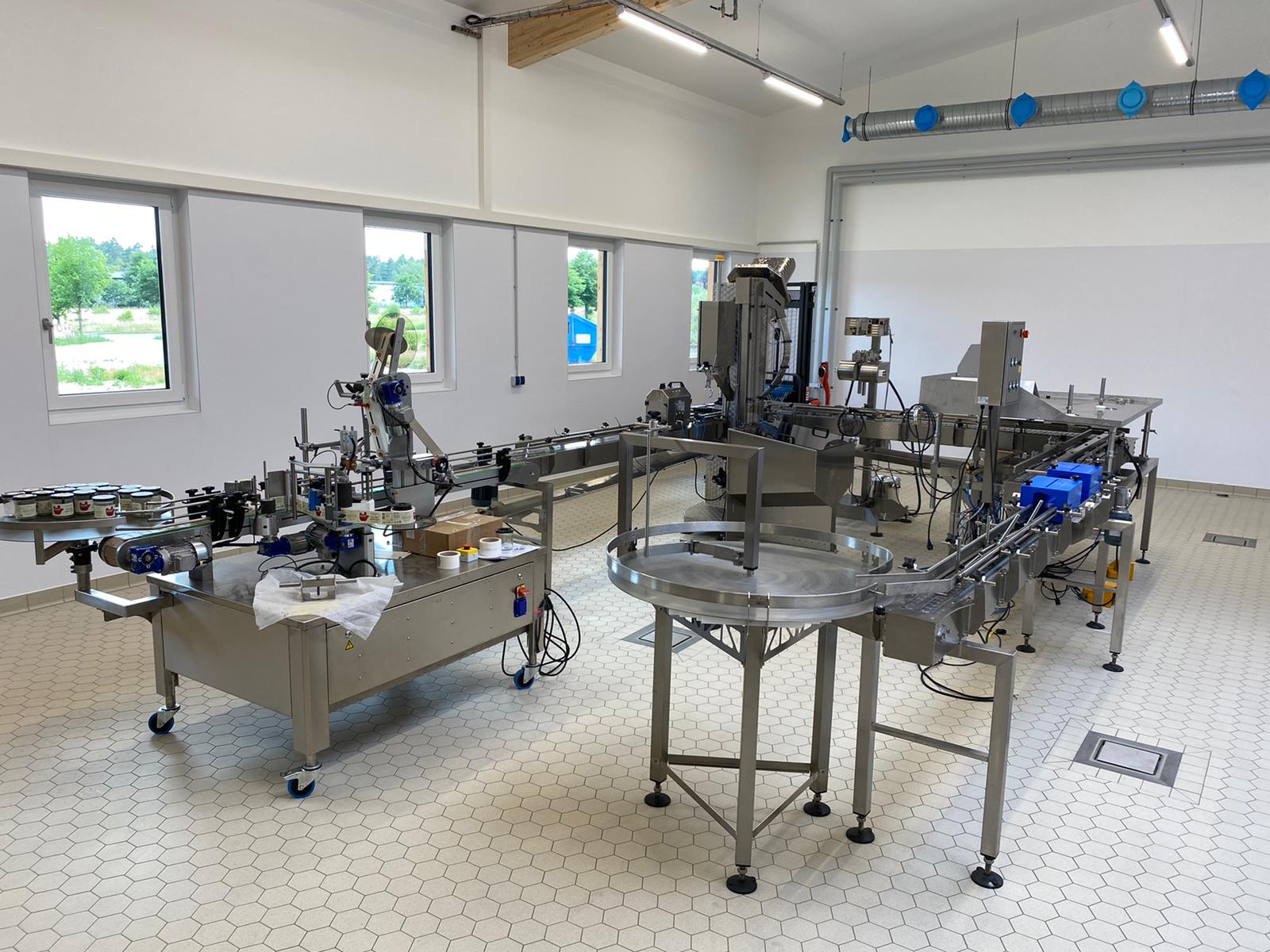